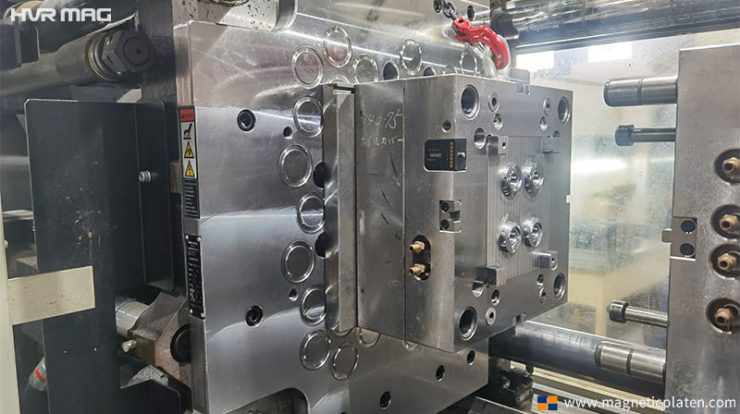
Plastic injection molding is a highly versatile process to produce complex shapes and parts with a high degree of accuracy and consistency. Injection molding machines have varies of size and capacity. They typically consist of a hopper, a heating unit, an injection unit, and a mold clamping unit. They can manufacture a wide range of products, including automotive parts, medical devices, toys, household appliances, and consumer electronics. However, the precision and quality of injection moulded products are affected by various factors. Such as the injection moulding machine, the mould and the clamping method of the mould.
Mold Clamping Method
The mould clamping device is also very important. Because the clamping method of the injection mould will affect the quality of the injection moulded product. There are usually two types of clamping methods for injection moulds: direct clamping and indirect clamping.
Direct clamping: Direct clamping means that the two halves of the mould are directly fixed to the clamping plate of the IMM through the mould clamps. This type of clamping is usually used for smaller moulds or simple injection moulded products. The advantages of direct clamping are strong clamping force and stable mould fixation. However, direct clamping may lead to deformation and stress concentration in the mould. Which may affect the dimensional accuracy and surface quality of the injection moulded product.
Indirect clamping: Indirect clamping means that the mould is fixed to the clamping plate of the injection moulding machine by means of a mould holder or a mould plate. This type of clamping is usually used for larger moulds or complex injection moulded products. The advantage of indirect clamping is that it can reduce the deformation and stress concentration of the mould. And improve the dimensional accuracy and surface quality of the injection moulded products. It also facilitates mould replacement and adjustment.
The selection of the appropriate clamping method needs to be decided according to the specific injection mould and product requirements. The clamping method of the mould should be able to provide sufficient clamping force to ensure the stability and accuracy of the mould. In addition, the clamping method should also take into account the size and weight of the mould. As well as the requirements of the injection moulded product to ensure optimum moulding quality and productivity.
Conclusion
The clamping method of the injection mould has a certain influence on the quality of injection moulded products. And the correct selection and use of the clamping method can improve the dimensional accuracy, surface quality and production efficiency of the products.
Magnetic clamping system is the most advanced mould clamping method at present. Its magnetic suction force is evenly distributed on the back of the mould. Which can minimize the degree of deformation and cavity area of the mould. As a result, the mould can be closed perfectly, producing products with better and more stable surface quality and precision.
Not only that, the magnetic clamping system can also greatly improve the efficiency of mould change. Also known as the Quick Mould Change System, it can clamp and release the mould in less than 3 minutes. A complete mould change can be completed in less than 30 minutes with adequate preparation at all stages of the process. For example, preheating the mould in advance and transporting it to the vicinity of the injection moulding machine reduces the waiting time during the mould change.
If you are looking for the solution to improve quality of injection moulding products and mold changing efficiency, welcome to visit the website or contact us.