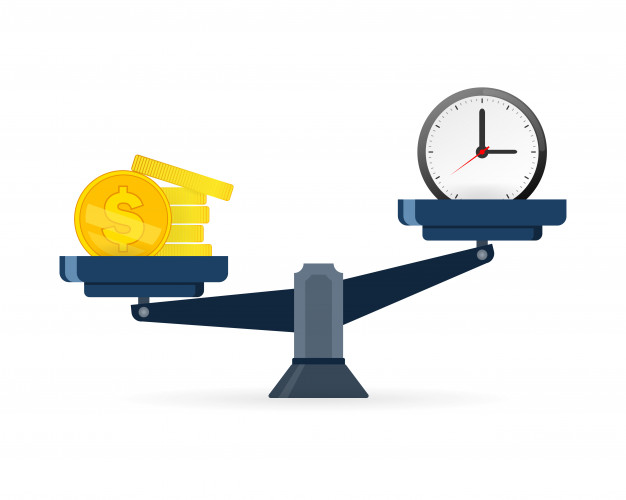
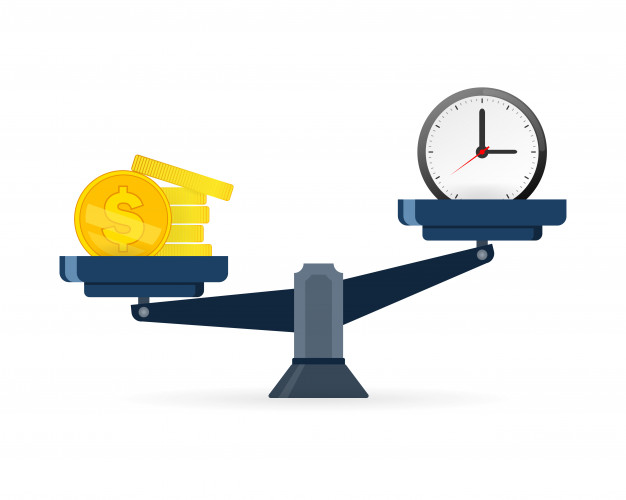
What is Cycle Time in Injection Molding?
Injection Molding Cycle time is the complete time taken or required to complete all the stages of the injection molding process. It is mainly made up of 3 stages:
Filling Time (Injection Stage) – heated material is fed via pressure into the mold and cavities
Packing time (Holding Stage) – when all material for a cycle has been fed into the mold, and continued pressure is applied to ensure that cavities are completely filled and any potential shrinkage of the material as it cools is addressed
Cooling time (Cooling Stage) – when the material cools to a solid form and pieces are ready to be ejected
Basically, it can be regarded as the time between mould close and mould open in a production cycle. Each of these steps has potential efficiencies that can reduce overall cycle time.
Importance of Cycle Time in Injection Molding
As cycle time plays a significant role in the injection molding process, in the quality of the parts produced, but especially the impact it makes on a company’s financial bottom line. Thus, optimizing a molding cycle can improve the production process, lower energy and labor costs, while also increasing profits.
An increase of additional two seconds on a given cycle may require extra hours of production, in turn taking away expected profit, and lessening the return on investment. Likewise, deducting seconds from a cycle time can lead to an increased number of parts produced in the same or less time, as well as increased profits by the thousands.
That being said, however, reducing cycle times is not always a “one size fit all” concept for mold makers when evaluating their production process and performance. Reducing cycle times may also lead to mold damage or compromise a part’s quality. Therefore it should be carefully gauged and adjusted before being put into practice.
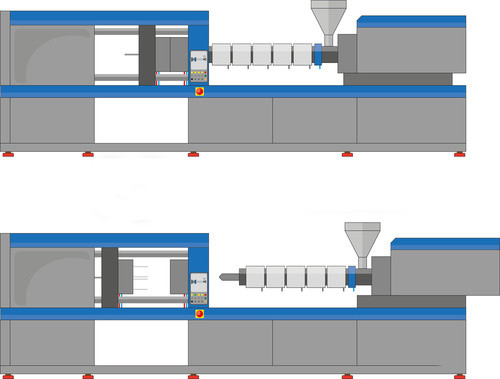
How to Reduce Cycle Time of Injection Molding Machine?
Injection molding process is a complex manufacturing activity, the efficiencty of which can be affected by many technical and design factors. There are many areas to consider when trying to reduce injection molding cycle time, such as:
Selecting the right machinery: The capability and performance of each plastic injection moulding machine and ensuring that it is correctly set up and optimized.
Choosing the right materials: The correct choice of materials for each application; different plastics for injection moulding have different melt temperatures, higher fill-pressure rates and flow characteristics. These will all affect the rate at which each part is formed.
Considering the design of the mould: The design and construction of the injection mould tool. The construction of the mould tool will be determined by the design of the part.
Other factors that can affect the cycle time are:
- Cooling time optimization of mold
- Reducing nozzle force, instead of retracting the nozzle completely
- Strategically setting pause time just enough to drop the part to eliminate excess movement
- Eliminate unnecessary movements
- Setting appropriate pause time to drop the part
- Open a mold only as far as needed
Understanding that cycle time is a key factor in determining the cost and time efficiency of creating a plastic component, can direct us to find possible & feasible ways on how to reduce cycle time in injection molding machine. And that can allow companies and factories to produce parts more efficiently at lower cost, while freeing up additional machine time.
Learn more about mold change for plastic injection molding machine, feel free to leave us a comment or welcome to visit our website:www.magneticplaten.com