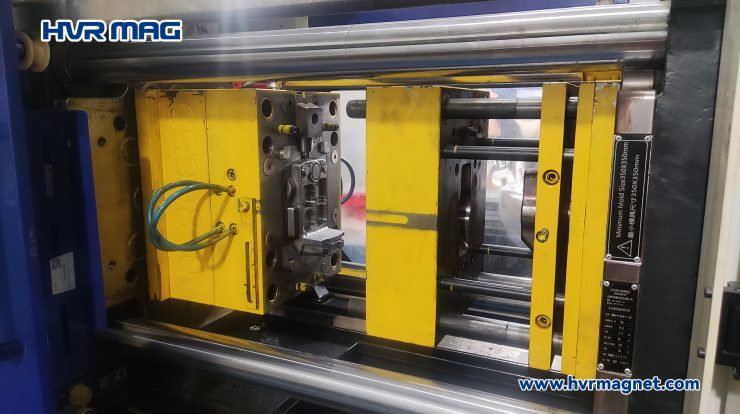
Injection molding machines consume a considerable amount of energy during operation. Implementing energy-efficient equipment, optimizing production processes, and using energy-saving technologies can significantly reduce the energy consumption associated with injection molding, leading to lower carbon emissions and operating costs. Magnetic platen, short for electro permanent magnetic platen, is also know as magnetic clamping system. One of its advantages is environmentally friendly.
Why is magnetic platen energy-saving?
Little energy consumption: It takes no more than 3 seconds to activate magnetic platen and electricity is required only during magnetization or demagnetization, making it the most energy-saving device.
All-electric: This all-electric system will not have hydraulic oil leak or produce consumable materials, causing no pollution to injection molding machine. With such feature, magnetic platens are widely used in medical and optics injection molding.
Low carbon: This platen does not use power while operating, so there is no heat and no noise.
How does magnetic platen reduce emission?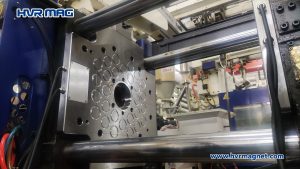
Long lifespan: The traditional clamping method is to press several clamping modules on the mold bottom plate, so mold opening and deformation frequently occur. In contrast, the total adsorption force of magnetic platen comes from the magnetic poles covering the whole platen, attracting the mold evenly. Even after long-term use, it can keep the mold from deformation. Thus, prolongs the lifespan of the mold and reduces mold trimming, decreasing maintenance cost directly.
High yield: The stable and uniform clamping force of magnetic clamping system minimizes the deformation and cavity of injection mold, resulting in firm mold closing. This produces products with smoother surface and better quality.
Reducing inventory: For plastic industries, one of the biggest problems is the imbalance between production capacity and order amount. When the efficiency of mold changeover is greatly improved, the injection molding production line can respond more quickly to the market requirement. Quick mold change system helps to increase production capacity to meet schedules, playing a key role in reducing overall manufacturing costs.
Conclusion
Integrating eco-friendliness into injection molding processes promotes sustainability, reduces environmental impact, conserves resources, supports regulatory compliance, and meets the growing demand for environmentally conscious products.
If you wonder whether magnetic platen is suitable for your business, please contact HVR MAG at export@hvrmagnet.com. We provide professional and detailed consultation based on your production demand.