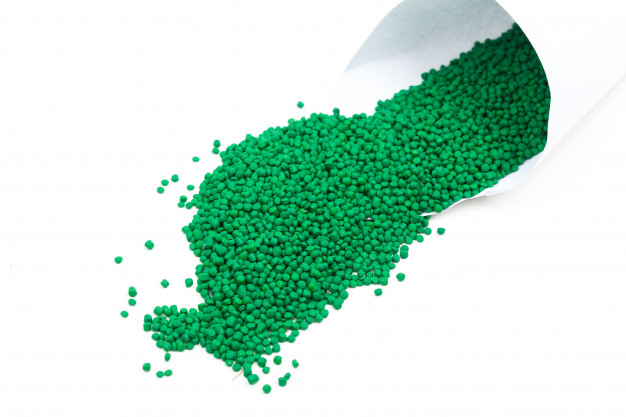
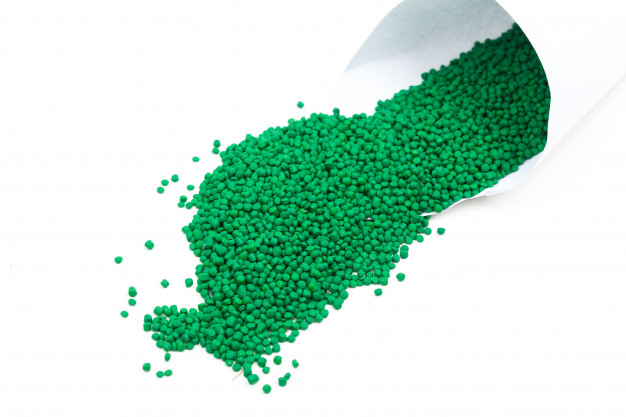
How will injection molding rate affect your plastic injection molding process? To answer that question, first, we need to figure out the following terms related to injection injection: injection rate, injection speed and injection time.
The injection rate of an injection molding machine, refers to the volume of molten plastic that is injected in one second, cm3/s, namely the volume flow rate that can be achieved per unit time at the time of injection. While the injection speed means the speed of forward movement of the plunger, mm/s, at which the screw or plunger moves during injection.
(Most often, these two terms are mixed up by people who think they’re simply the same.)
As to the injection time, it’s a lot easier to understand – refers to the shortest time taken by the screw or plunger to complete the longest injection stroke, or the shortest time needed for the complete injection of the material with injection capacity and volume.
What needs to be noted is that, the injection speed is typically set at the minimum value required to completely fill the component without any defects. Normally, at higher injection speeds, the risk of a notch and stress peaks developing on the surface is reduced. Generally, under the premise of not causing side effects, high-speed mold filling should be performed as far as possible to ensure the molding strength and appearance quality of plastic pieces, with lower pressure to reduce their internal stress and improve their strength.
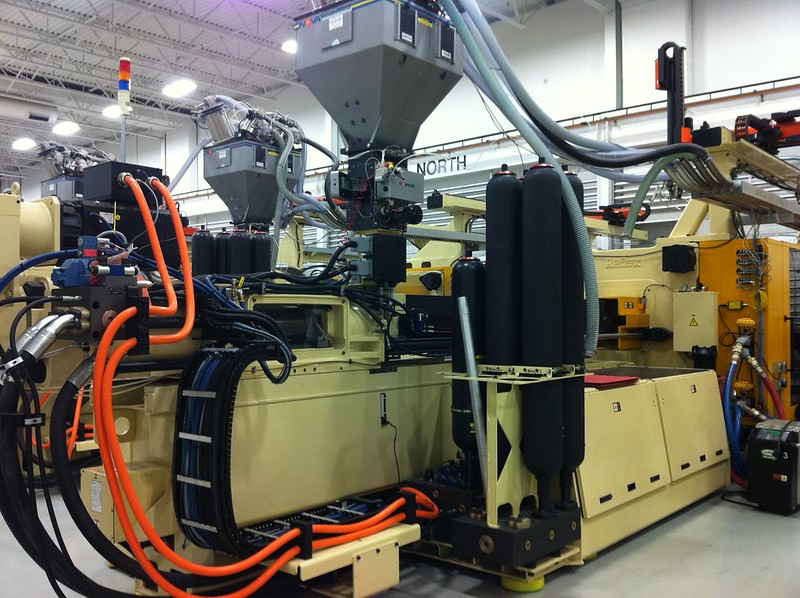
Yet too high an injection speed will result in flash and gate blemishes due to powder/binder separation and potentially voids, if the injection is too fast to allow the air inside the cavity to escape at the mold vents. If the injection speed is set too low, it will result in surface imperfections such as flow lines, poor weld lines, and incomplete fill.
To sum up, setting an ideal injection rate of IMM, is like determining an appropriate foothold between product quality and production quantity of injection molded parts. It should allow the most evenly molted plastic to be injected to the mold within the shortest time, and solidified in a uniform state under the condition that the appearance quality of the plastic and the structure of mold remain unchanged.
Welcome to visit our website to learn a new way to reduce your mold changing time – magnetic quick mold change system for injection molding machines.