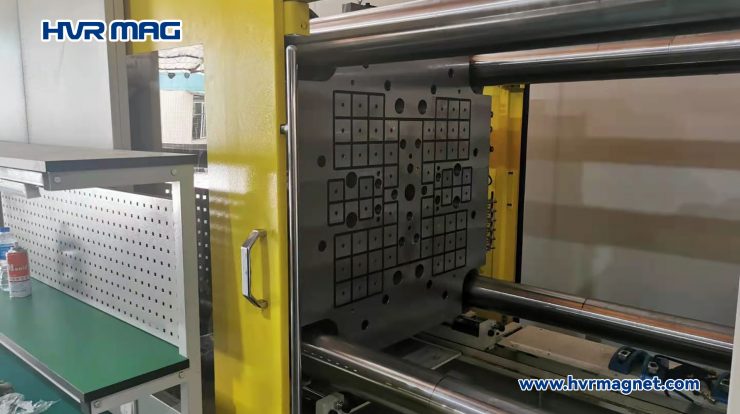
Injection molding is a widely used manufacturing process in which molten material is injected into a mold cavity, resulting in the production of various products. The efficiency and productivity of injection molding depend on several factors, including the clamping force and speed of mold closing and opening. Traditional hydraulic systems have been commonly used to achieve these functions. However, with advancements in technology, the magnetic platen is gaining popularity due to its ability to save time in the injection molding process.
Wide range of applicability of magnetic platen
Usually, molds of different sizes need to be installed on machines with different tonnages for production. However, molds can be clamped onto the magnetic platen without any adjustments despite the size, as long as the mold’s weight is below the limit. There are no restrictions on horizontal, vertical, or even oblique installations because the magnetic platen is entirely open. Thus, larger molds can be installed on the machines, which significantly saves investment in machinery.
Lengthen the life span of molds, and improve product quality
Since the surface of the magnetic platen is entirely arranged with magnetic poles, which is also the clamping point, the clamping pressure is uniform. During the mold opening and closing process, the mold won’t experience stress deformation, which results in better quality and higher consistency of the injection products, while prolonging the mold’s life span. In comparison, hydraulic pressure plates only exert force on the periphery of the mold, and the mold’s center doesn’t receive any clamping force. It may cause deformation, leading to low-quality injection products, poor consistency, and more wear, reducing the mold’s life span.
Low maintenance, high reliability
The magnetic platen clamps the mold using the magnetic force of a permanent magnet. There are no moving parts inside the platen, causing no mechanical work wear or tear. It only uses a power supply for 1-3 seconds during the mold’s loading and unloading, which enables the magnetic platen to have a long life span. After a one-time installation and debug, there is no need for regular machine downtime for maintenance and repair, and no vulnerable parts, greatly reducing downtime and maintenance costs.
Environmentally friendly
The magnetic platen doesn’t require any power supply during its operation, as it uses the permanent magnetic force. This means there is no energy consumption or noise generated during its operation, making it an environmentally friendly solution. There is no need to remove the mold after powering off, and there will be no pollution to products, equipment, or the working environment. Thus, magnetic platens are safe, energy-saving, and cost-effective.
Conclusion of magnetic platen
In conclusion, magnetic platens save costs in injection molding in many different ways. They have a wide range of applicability and do not require any adjustment, lengthening the life span of molds and improving product quality. They are also low-maintenance, reliable, and energy-saving, which makes them a beneficial environmental solution for the injection molding industry. For more information, please contact HVR MAG at export@hvrmagnet.com.