
The Magnetic Clamping Device is the most advantageous injection mold clamping tool available. It can help reduce mould change time and increase productivity. Here I will introduce you to the design principle of magnetic clamping device.
Structure of injection moulding machine
First, let’s see how an injection moulding machine works. The raw material for the plastic products is fed through a hopper into barrel. Inside the barrel, the plastic granules are heated, melted and stirred well. It then passes through the nozzle into the mould cavity, where it is cooled and moulded. Once you understand how an injection moulding machine works, its structure becomes very clear.
Mould is the core part during injection moulding process. It is held in the centre by the fixed plate and the moving plate. The moving plate moves towards the fixed side as the machine performs the injection process. Until the mould is tightly closed – ensuring that the product is evenly moulded. After the product has cooled, the moving plate moves back. The product can be removed then.
Problem that needs to be solved
If there is a slight loosening or misalignment of the mould during closing and opening, this can lead to wear and distortion of the mould. This not only shortens the life of the mould, but also affects the quality of the product. Therefore, the way the mould is fixed is very important. The injection moulding machine comes with a back plate that can only be fixed with bolts. On the one hand, the bolts tend to loosen over time. On the other hand, such a fixing method makes it very inconvenient and time-consuming to change the mould, which affects productivity.
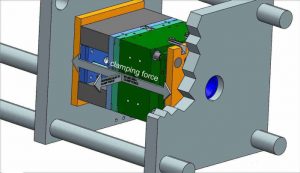
As a result, there are a number of different mould clamping and quick mold change systems on the market. The most common at present are hydraulic and magnetic type. The magnetic clamping device is very simple. Two magnetic plates are mounted on the back plate on each side of the injection moulding machine. The mould is held on the magnetic plates by a strong magnetic suction of 16 kg per cm2. The moulded product has a better consistency because the two sides of the mould are perfectly parallel and the force is evenly distributed over the entire back of the mould.
Design principle of magnetic clamping device
The magnetic plate is evenly spaced with a number of poles containing electrically switched permanent magnets. You can switch between magnetisation and demagnetisation in 0.2 to 2 seconds when changing moulds. Once magnetised, no power is required to maintain the magnetic force. So the magnetic clamping device is very energy efficient and doesn’t get hot.
The magnetic clamping device has a very good safety feature. We have fitted the magnetic plate with temperature detection, distance detection, misalignment detection and magnetic flux detection. These tests help you to monitor the position and status of the mould. This data can be viewed on the control panel and an automatic alarm is generated if the data is abnormal.
Advanteges of magnetic clamping device
The magnetic clamping device is made of steel for strength and durability. The permanent magnetic material inside will not reduce the magnetic force by more than 5% in 10 years as long as it is at normal operating temperature. The magnetic clamping device therefore requires virtually no maintenance. The only maintenance required is to keep the magnetic template clean each time the mould is changed.
Overall, the magnetic clamping device can be perfectly adapted to all types of injection moulding machines. There is no need to modify the back plate of the injection moulding machine and there is no obstruction around the mould. It is also energy efficient and maintenance free. There is no leakage of contaminants. It ensures safe production of the mould and the injection moulding machine, while improving productivity and product quality. It is by far the most recommended clamping device for injection moulds.
If you are interested about HVR MAG and our mold clamping system, please contact us at: export@hvrmagnet.com