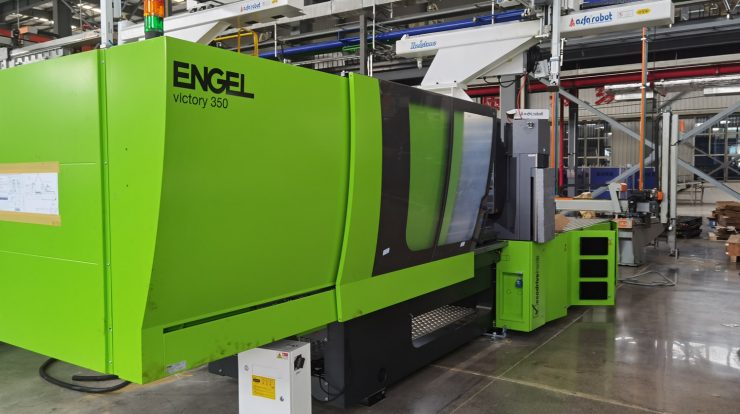
With the rapid development of network and artificial intelligence, more and more industries are being subverted and more and more occupations are being replaced by intelligent devices. With the advent of Industry 4.0 era, what is the future of plastic injection molding engineers?
Let’s take a look at what an Industry 4.0 plastic injection molding workshop is or will be like in the future:
After the injection molding production receives the order demand, the system will automatically arrange the machine and calculate the amount of raw materials used, and then the automatic logistics flatbed truck will go to the raw materials warehouse to collect the raw materials and transport them to the centralized drying room for dehumidification and drying.
The dehumidifying and drying machine will automatically scan the raw material information, get the drying time and temperature and set automatically. After the drying is completed, the centralized material supply system will input to the corresponding injection molding machine hopper through the material supply pipeline.
While the material is drying, the automatic logistics mold loading trailer will go to the mold storage area to pick up the mold and then perform automatic mold loading. The current development of quick mold change system has long been able to standardize and automate the mold loading process. After the mold is positioned into the mold base of the injection molding machine, the mold is automatically changed by magnetic clamping or hydraulic clamping system. The robot then connects the integrated water circuit of the mold temperature controller to the integrated water circuit on the mold, or it can also be plugged in for power supply.
After that, the injection molding machine starts the automatic mold thickness adjustment system to adjust the mold thickness. Then the injection molding machine will be automatically adjusted and the mold will be test run, and if there is any abnormality, it will automatically alarm and stop.
After punching out the sample, it is transmitted to the automatic 3D scanning inspection station for scanning and comparing with 3D data, and the comparison result is generated and fed back to the injection molding machine system. For example, if there is a lack of glue or trapped air, the size is small or large, the injection molding machine will automatically adjust the injection speed and holding pressure and other related parameters, and re-sample.
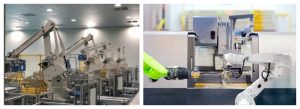
For the parts with appearance requirements, they will be automatically sent to CCD for appearance comparison check. Then the CCD will feedback the inspection results to the injection molding machine system, such as flow marks, the injection molding machine will automatically adjust the corresponding parameters according to the results and re-prototype according to a certain amount ratio.
Regarding the feasibility of automatic tuning of the injection molding machine, the current technology is still under development, and the feasibility of the future is still very high. After the debugging, the debugging samples are automatically put to the scrap area by the robot. Then the mass production starts and the automatic packing machinery is boxed and packed, and sent to the finished product warehouse by the automatic logistics truck.
Based on the current state of development of industrial technology, it can be imagined that the future automation of the injection molding workshop, or even full automation, is definitely no longer a myth! Of course, the future may also develop more environmentally friendly and economic new materials, can replace plastic products. Everything is still uncertain. But it seems sure that fewer and fewer injection molding engineers will be needed in the workshop in the future.
Back to the industry 4.0, about the future of plastic injection molding engineers, what do you think of it? Welcome to leave a message in the comment section. Don’t forget, HVR MAG, can be at the forefront of quick mold change technology for plastic injection molding machines, if you have a need for magnetic platens, welcome to inquire us: export@hvrmagnet.com
Note: Reference from the author Delta’s article on “Automation of Injection Molding Machines in Industrial 4.0 Era”.