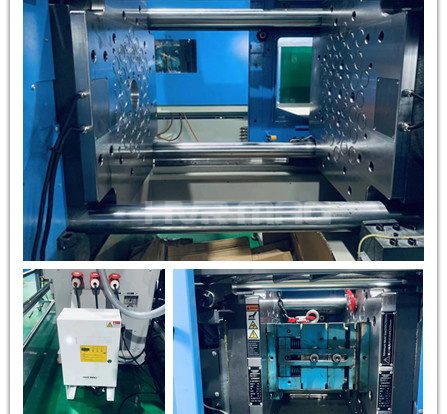
As the world’s population continues to rise, along with an increasingly aging population and a growing number of patients with chronic diseases, the medical industry is becoming increasingly important, as well as the medical plastic injection molding industry.
Current status of medical plastic injection molding
The medical plastics industry covers a variety of molding processes such as extrusion, blow molding, and injection molding. According to relevant statistics, medical plastic products produced by injection molding technology account for more than 70% of the entire production volume. It is the most important form of medical plastic product production. Medical injection molding products can be broadly divided into the following categories:
1. Equipment, such as Petri dishes; 2. health care, such as fitness equipment; 3. organs, such as plastic joints; 4. surgery, such as cervical hooks; 5. instruments, such as guide dilators; 6. testing, such as cell culture vessels; 7. testing, such as insulin measuring pens, and so on.
The medical injection molding industry has grown very rapidly in recent years. On the one hand, the development of global healthcare. On the other hand, since the outbreak of the coronavirus epidemic, the medical and health care industry has been pushed to a new wave.
How does magnetic quick mold change help?
I. Manufacturing Environment and production equipment
The injection molding workshop in the medical industry usually requires a fully enclosed clean and dust-free workshop with high-powered air conditioning equipment to eliminate harmful gases in the workshop in time to ensure constant temperature, constant humidity, and clean air.
The principle and purpose of medical injection molding machines are to reduce the contamination of products while reducing the emission of exhaust gas, dust, and other sources of pollution to the clean room. The layout of the injection molding machine and the clean room has two forms mainly:
(1) Place the whole injection molding machine in the clean room. This layout will increase the cost of cleanliness due to the large clean room space.
(2) Only the clamping mechanism is placed in the clean room, only the mold space is purified, and the products are transported to the clean room assembly line for post-processing through the assembly line.
The magnetic mold clamping system can better ensure cleanliness than the hydraulic mold clamps can do. Since the latter requires a regular oil change and has a risk of oil leakage. The magnetic platen is made of steel and the whole-steel surfaces can be cleaned very easily and quickly. The maintenance is also very convenient. Besides, for smart manufacturing, the magnetic mold clamping system can be better adapted to the automation production system.
2. The molds
Medical plastics have high requirements for mold material, size, ejectors, etc. And the magnetic mold clamping system has a uniform distribution of magnetic force to the mold back. Hence it avoids mold deformation. What’s more, except for the location ring, it requires no mold change but is compatible with various mold sizes.
3. Processing technology
The most common quality problems in the medical industry include product size, raw edges, deformation, and internal stress of the product. The magnetic mold clamping system, with its 3-minute mold change cycle, stable structure, and energy-saving characteristics, can minimize mold and injection molding machine failures, and increase capacity and efficiency.
You are interested in magnetic quick mold change for medical plastic injection molding? Please contact us: export@hvrmagnet.com. HVR MAG is a professional manufacturer specializing in the electro-permanent magnet for over 12 years, leading China magnetic industry.