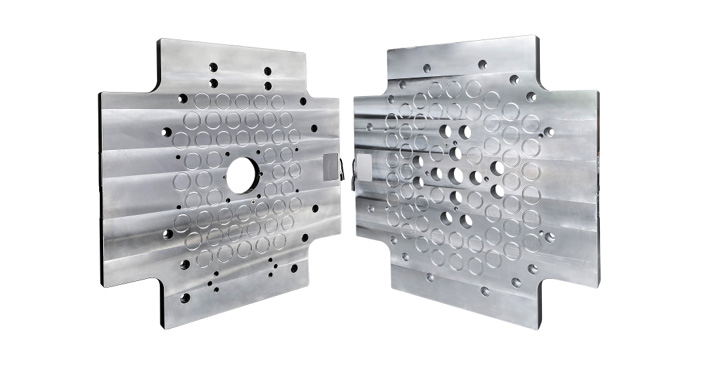
Introduction of magnetic platens
Magnetic platens, or sometimes referred as magnetic clamping plates, are mounted in injection molding machines or metal stamping press machines for quick mold / die change. No clamps required, in comparison to mechanical clamping or hydraulic mold-clamping approaches, magnetic platens allow very fast mold / die changing as they use strong magnetic force to uniformly clamp the mold / die to perform a quick mold / die change process. Generally, they come in a set, one fixed (stationary) platen and one movable platen.
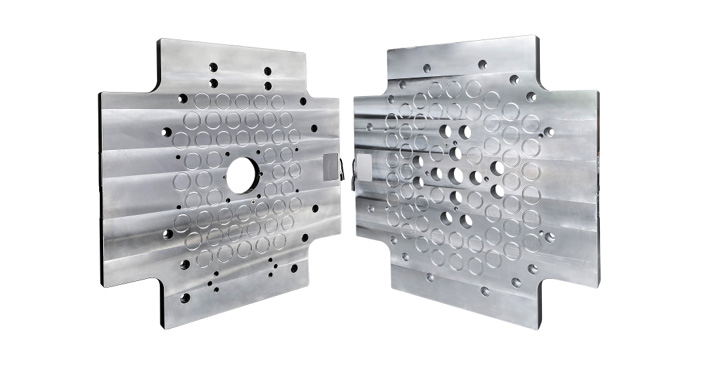
Magnetic platens by HVA MAG, utilizes electro permanent magnetic clamping technology that develops very high magnetic force. Electric pulse is only required to activate & de-activate the magnets inside the platen, which means that the magnetic force remains in case of a power failure. It doesn’t requires power once it is magnetized.
Advantages of HVR MAG magnetic platens:
1. Fast clamping
2. No deformation – uniform magnetic field, uniform clamping force across the entire rear of mould
3. Maintenance Free
4. Drastic reduction of machine downtime and improved productivity
5. Very safe – electro permanent magnetic force remains, therefore no need to worry about the mold / die falling off in a power failure
6. Energy saving – zero power consumption during work
7. More flexibility as shorter runs can be planned as a result of speed-up of changeover.
For companies who have frequent mould / die changes, especially with heavy tools, magnetic platens can eliminate mold change bottlenecks by removing and installing a new mold in several minutes. Due to the advanced clamping technology employed, HVR MAG magnetic clamping plates constitute an efficient magnetic mold / die clamping system for plastic injection molding machines. Moreover, we have platens for sale with ranging thickness of 35mm, 46mm, 51mm for injection molding machines with different tonnages. Learn more about magnetic clamping solution for quick mold / die change, welcome to visit our website.